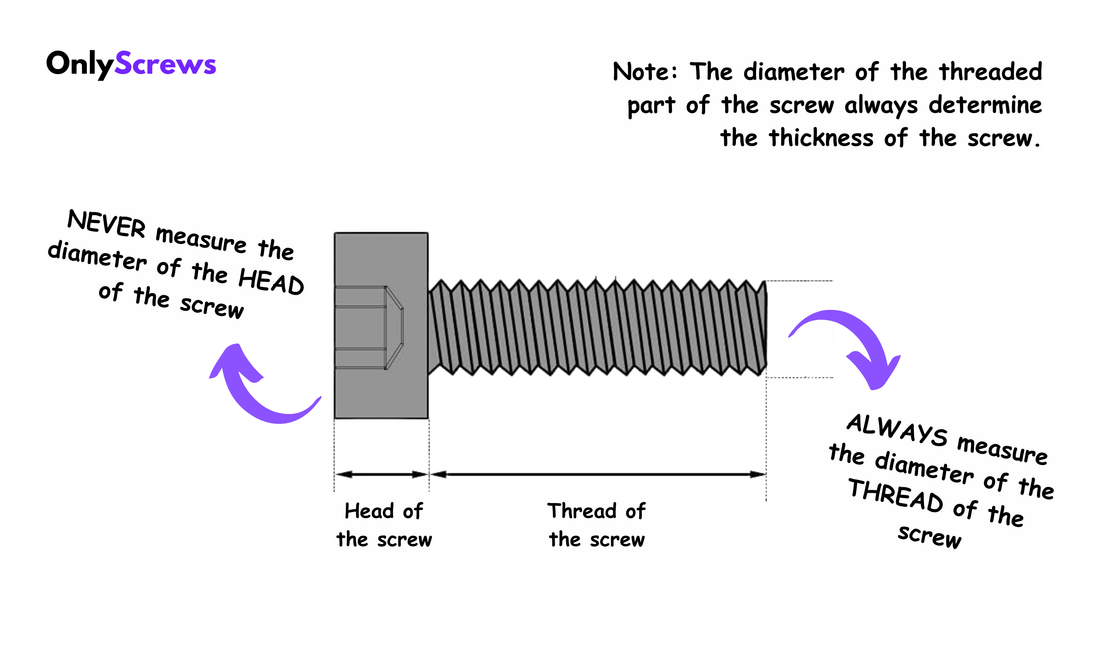
How to Measure the Diameter of a Screw (The Right Way!)
Share
In this blog, we will walk you through the simplest and most accurate way to measure the diameter of a screw and highlight the common mistakes to avoid.
The Correct Way to Measure a Screw’s Diameter
The key to measuring a screw correctly is to measure only the diameter of the threaded part, not the head of the screw. The head size can vary depending on the type of screw (e.g., flathead, pan head, hex head), manufacturer and the manufacturing standards of the screw. The diameter of the threaded portion remains constant for fitting into nuts or threaded holes.
You can check out our video guide as well.
Understanding Screw Diameter
The diameter of a machine screw is typically measured in one of the following ways:
- Major Diameter (Outer Diameter) – This is the widest part of the threads and is the measurement commonly used to specify screw size.
- Minor Diameter (Root Diameter) – This is the narrowest part of the threads and is usually measured for internal threading purposes.
- Pitch Diameter – This is used in more technical applications but is not commonly needed for simple identification.
For practical purposes, the major diameter is what most people need to measure when identifying a machine screw.
Tools You Need
To measure the diameter of a machine screw accurately, you will need:
- A caliper (digital or vernier) – The most precise tool for measuring screw diameter.
- A ruler – Useful for rough measurements but not always reliable for small screws.
- A thread gauge (optional) – Helps in identifying thread pitch along with the diameter.
Step by-Step Guide to Measuring Screw Diameter
1. Use a Caliper for Accuracy
- Open the caliper jaws and place the threaded part of the screw between them.
- Ensure the caliper touches the outer edges of the threads without applying excessive force.
- Read the measurement from the caliper’s scale.
Example: If the caliper reads 4mm, the screw is M4 (for metric screws). If it reads #8 (0.164 inches), then it's a #8 machine screw (for imperial screws).
2. Measuring with a Ruler (Less Accurate Method)
- Place the screw against the ruler, aligning it with the 0 mark.
- Measure across the widest part of the threads.
- Round to the nearest available size in the screw chart.
This method can work for larger screws but is not recommended for precision measurements.
3. Check the Measurement Standard (Metric vs. Imperial)
Machine screws come in metric (millimeters) and imperial (inches) standards. If you measured in inches, compare it to a standard screw size chart to determine the correct designation.
Common Mistakes People Make
❌ Measuring the diameter of the head instead of the threaded part
Many people mistakenly measure across the head of the screw instead of the threaded part. (This is the most common mistake. So be double cautious!!)
❌ Using a Ruler for Small Screws
For screws smaller than 5mm, a ruler can be misleading as it’s hard to align the measurement correctly. Always use a caliper for small machine screws.
❌ Confusing Screw Length with Diameter
Some people mix up length and diameter when identifying screws. The diameter refers to the thickness of the screw, not its length.
Conclusion
Measuring the diameter of a machine screw the right way can save you from mismatched hardware and assembly headaches. Always aim to use a caliper for precision, and avoid common mistakes like measuring across the threads incorrectly. Whether you’re working with metric or imperial screws, having the correct diameter ensures a perfect fit every time.